長らく大量生産の仕組みから脱却できていなかったアパレル業界にも、ついに「少量生産」の時代がやってきた。その流れを支えるのは、服飾用の「3Dマシーン」の存在だ。
在庫を極限までおさえて、徹底的に無駄をなくす新たな生産システム。大量生産にてコストを削減する必要がないということは、これまでのより安い労働力を求めてのアウトソーシングの必要性も低くするということ。アパレル業界の新たな生産システムは、「製造を再び都市へ、消費の地に戻そう」という動きも起こしつつあるのだ。
最新テクノロジーで「オンデマンド」生産。在庫を極限まで抑えて衣類ゴミを減らす
ビールも食品も小物も、「やっぱり丁寧な手仕事、少量生産がいいよね」ということになって久しい。はじめこそ、それはどこか懐古的なものだったかもしれない。しかし、「サステナブル」「製造過程の透明性」など、倫理的に正しいかどうかの価値判断をなおざりにできなくなったいま、少量生産を支持することは時代の主流になりつつあるように思う。その流れの根本を支えるのは、“匠の手仕事”並の性能を持った、最新テクノロジーだ。
いままでにも、ヒープスでは、ファッション業界の“余り物(サンプル)”を社会貢献へと有効活用したり、ファッションの作り手がだす布の切れ端を回収するなど、ファッション業界のゴミ問題に立ち向かうアクションを取り上げてきたが、今回は、そもそも余剰在庫が多すぎるという、アパレル産業の根本的な問題を解決しようと試みるスタートアップの話である。
昨年も、アパレル産業の在庫問題がいろいろと話題になった。トレンドをおさえた衣料品を、大量生産で安く消費者に届けることで人気を得たファストファッション大手の「H&M」が、約4200億円相当の売れ残り商品を抱えていることや、英国のハイブランド「バーバリー」が、約40億円相当の売れ残り商品を焼却処分したことなどが報道された(のちに焼却処分を今後は辞めることを表明)。廃棄焼却処分で発生するCO2(二酸化炭素)による、地球環境負荷の大きさはいうまでもない。
ファストファッションとハイブランド、どちらも売り上げの低迷、値引き、余剰在庫といった悪循環から抜け出せないのは、ひとえに「大量生産の仕組みから脱却できていないから」。そう話すのは、ブルックリンのサンセットパーク地区にスタジオを構えるニット会社「テイラード・インダストリー(Tailored Industry)」の共同創始者の一人、アンドレス・アルべス氏。
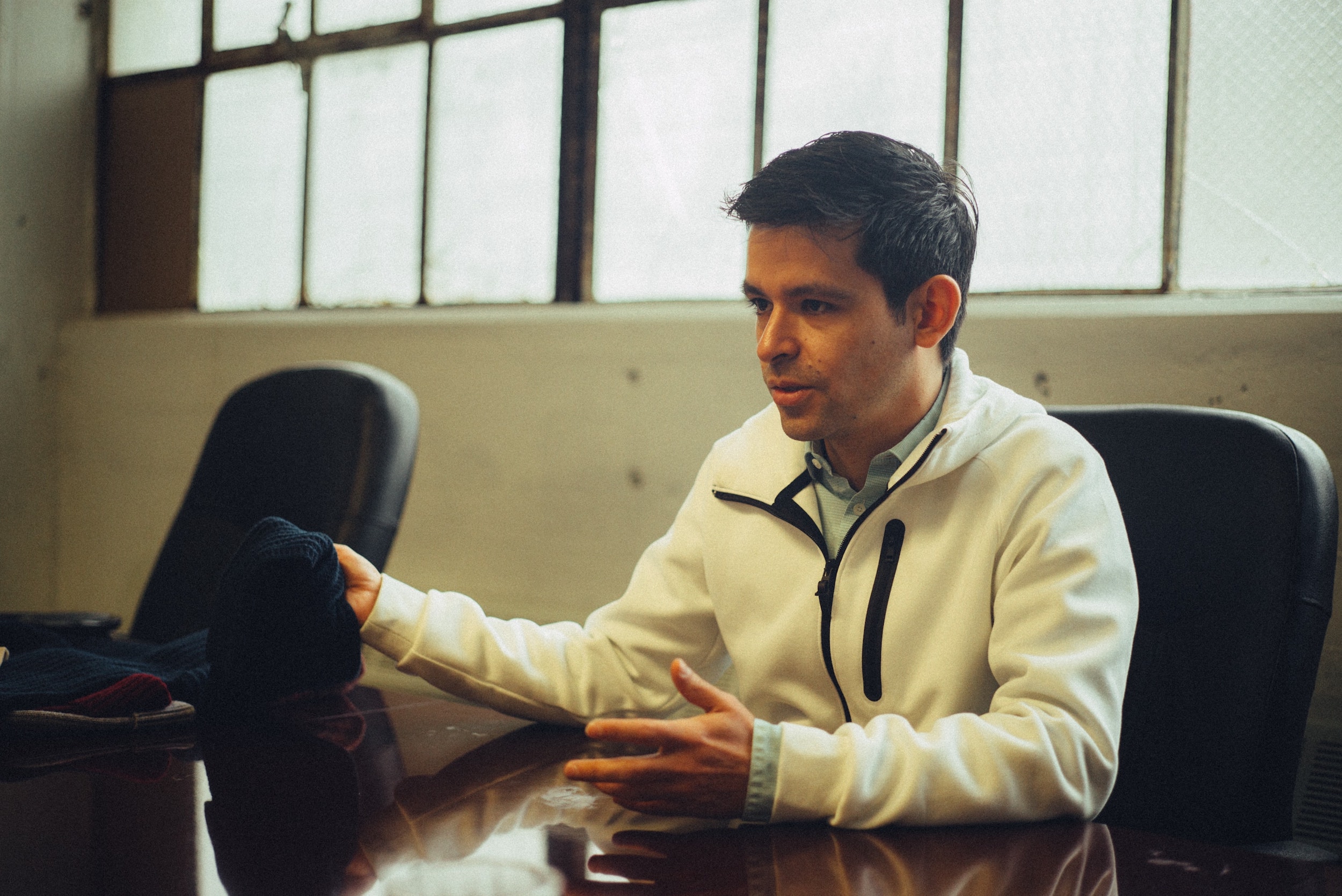
取材に応じてくれたアンドレス・アルベス氏。取材陣をスタジオに招いてくれた。
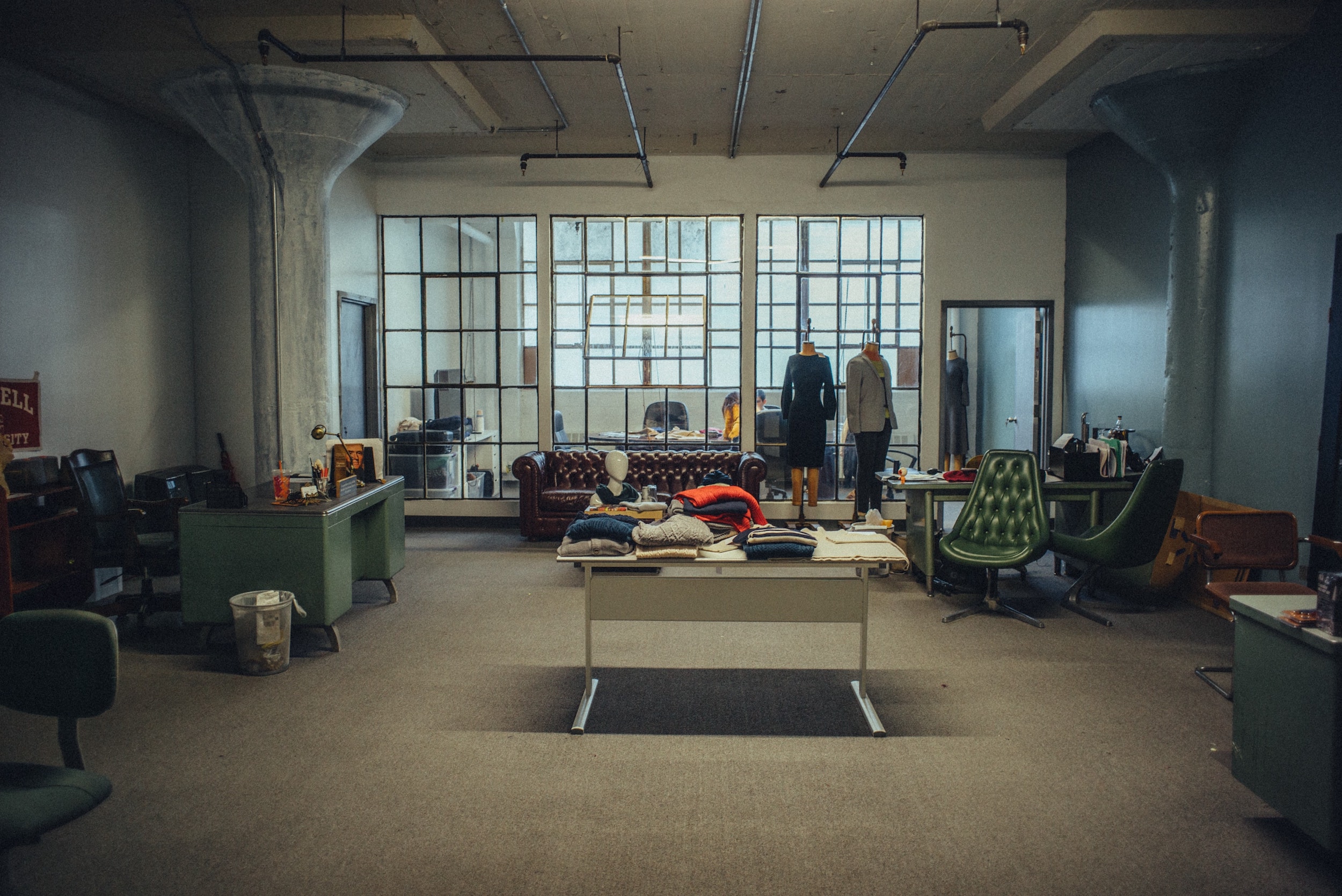
大量生産の狙いは、商品ひとつあたりの生産にかかるコストを下げることであり、その仕組みの特徴といえば、作業を細分化して、各工程の単純化をはかり、低賃金の労働力を活用できるようにすることにある。そのため、先進国の多くのアパレル企業が、自国よりもより安い労働力を求めて海外へと工場を移転させていった。
大量生産を前提としたラインでは大規模投資のもと製造ラインを構築するため、固定費が多くかかる。よって、工場の稼働率が低ければ製造原価が跳ね上がる。それを避けて、大量生産の効果を出すためには一定の生産量以上を確保しなければならない、というのが通説。これで、作った商品が売り切れればよいがそうもいかず。結果、余剰在庫が発生してしまう…という、この大量生産方式こそが、余剰在庫の問題の「悪循環の元凶」だという。
ならば、とテイラー・インダストリーが提唱するのは「オンデマンド(On-Demand)」生産だ。そもそも受注が入ってから生産すれば、在庫を抱えることも、売れ残りの処分に苦心することもない。言ってしまえば当たり前のことなのだが、それでは市場競争のスピードについていくことができないがゆえに、半年以上も前から企画やデザインを進めるのが常になっていた。
しかし、いまは「発達したテクノロジーがある」。彼らのいう「テクノロジー」とは、ホールガーメント機「3Dニッティング・マシーン」である。3Dニットと聞いてピンときた人も多いのではないだろうか。そう、ニット機の世界最大手、島精機製作所の名機だ。
島精機の「ホールガーメント(無縫製)」機は、その名の通り、襟元のラベルなどを除き、ニットそのものが完全無縫製で編み立てられている点に特徴がある。従来は、型紙に沿って前身頃・後ろ身頃・袖といったパーツを切り取り、裁断した複数の生地を縫い合わせ、ひとつの衣料に仕立ていたのに対し、この「3Dニッティング・マシーン」を使えば、型紙などを必要とせず、一着丸ごとを一気に立体的に編み上げることができる。よって、パーツを縫い合わせる必要がなく、そのぶん「発注から納品までの時間をより削減できます」。
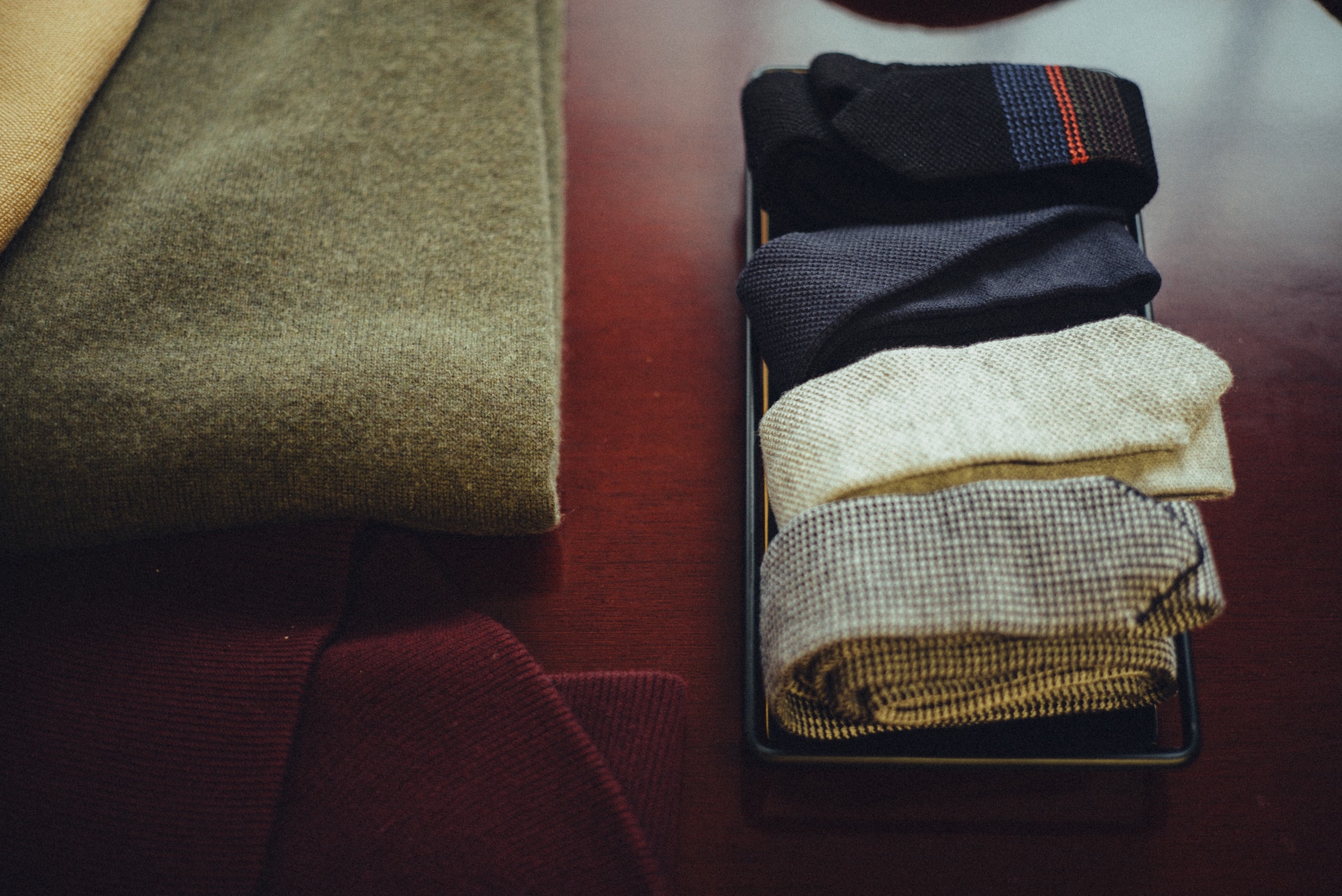
実際のプロダクトたち。
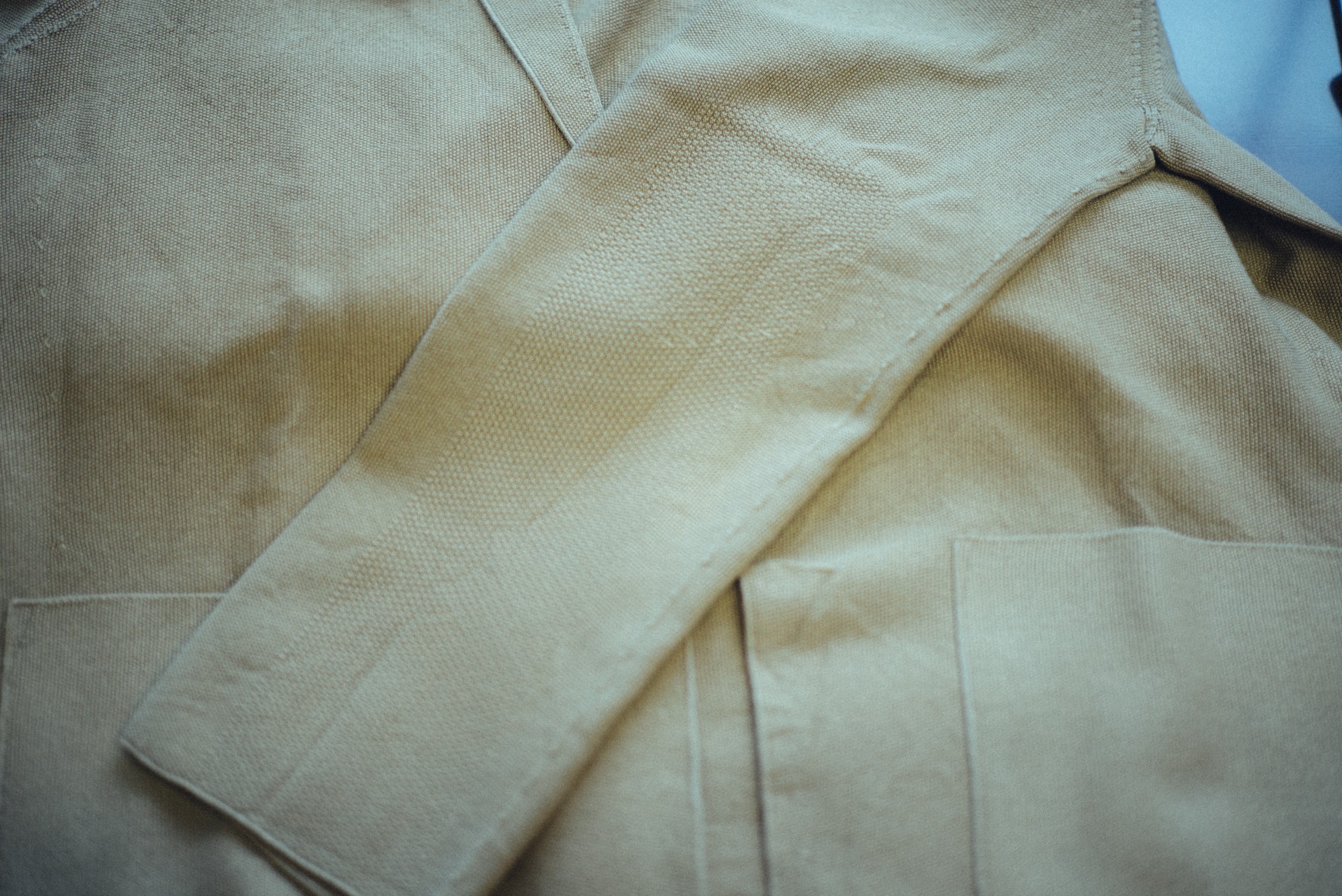
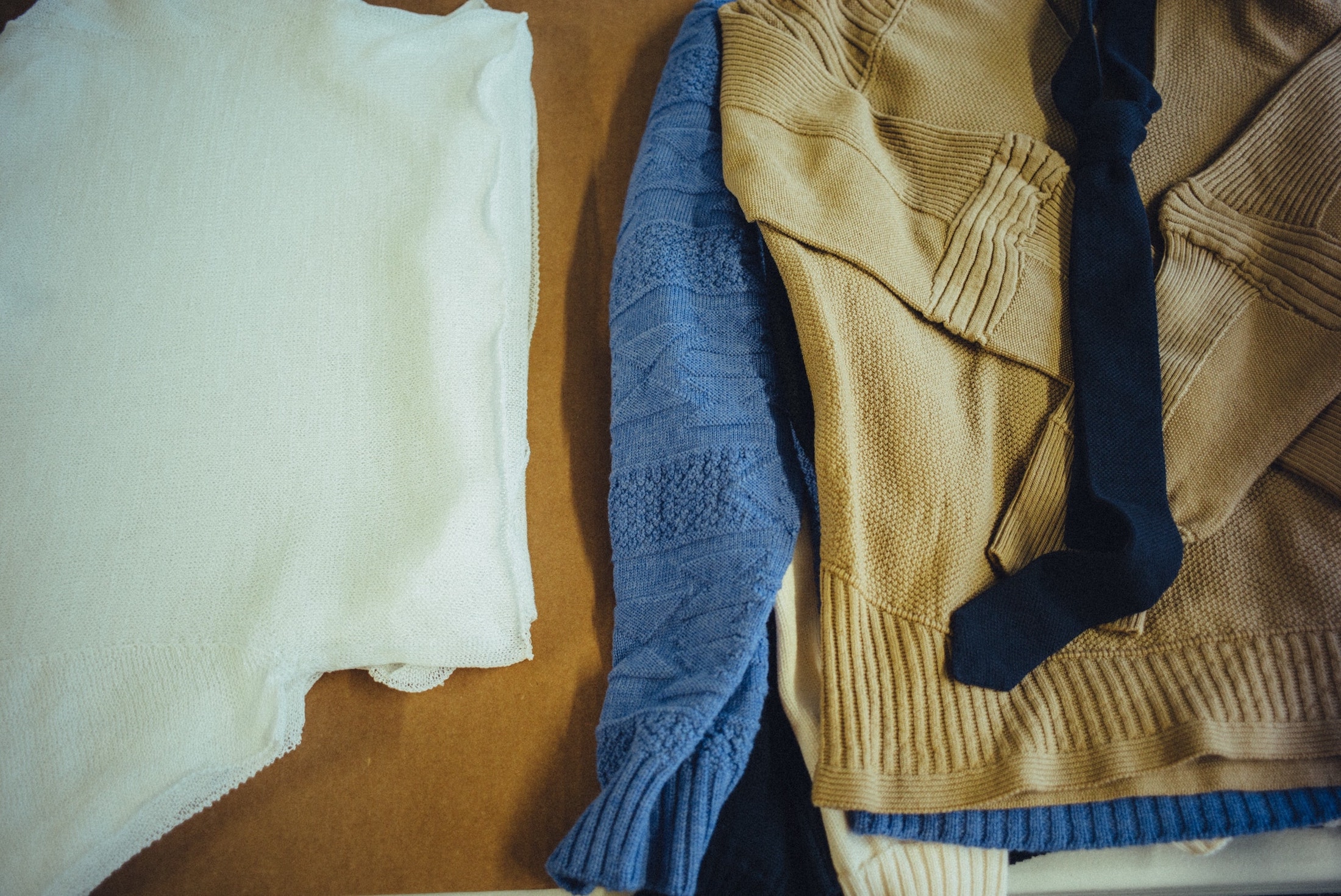
また、工程にかかる時間と労力を省けることに加えて「パーツを切り取る裁断工程が省けるので、裁ち落とし部分のカットロスがなくなります」。それは、衣類ゴミの削減になるのはもちろん、アパレルメーカーにとっても材料コストの削減というメリットに繋がると話す。
「流行先読み」が当たらない時代の救世主となるか
ホールガーメント機を使えば、たとえば、太めの糸を使ったトップスであれば、一着1時間以内で完成する。細めの糸を使ったブレザーやドレスは一着あたり約2時間。同じデザインのものは300着までであれば、発注から納品までに必要な時間は「だいたい2週間」だそうだ。
この機械と併用して、ソフトウェアも導入している。このソフトウェアにデザインを打ち込めば、フィッシャーマン(アラン)ニットのような入り組んだパターンも、バラつくことなく一貫した品質で生産可能だ。
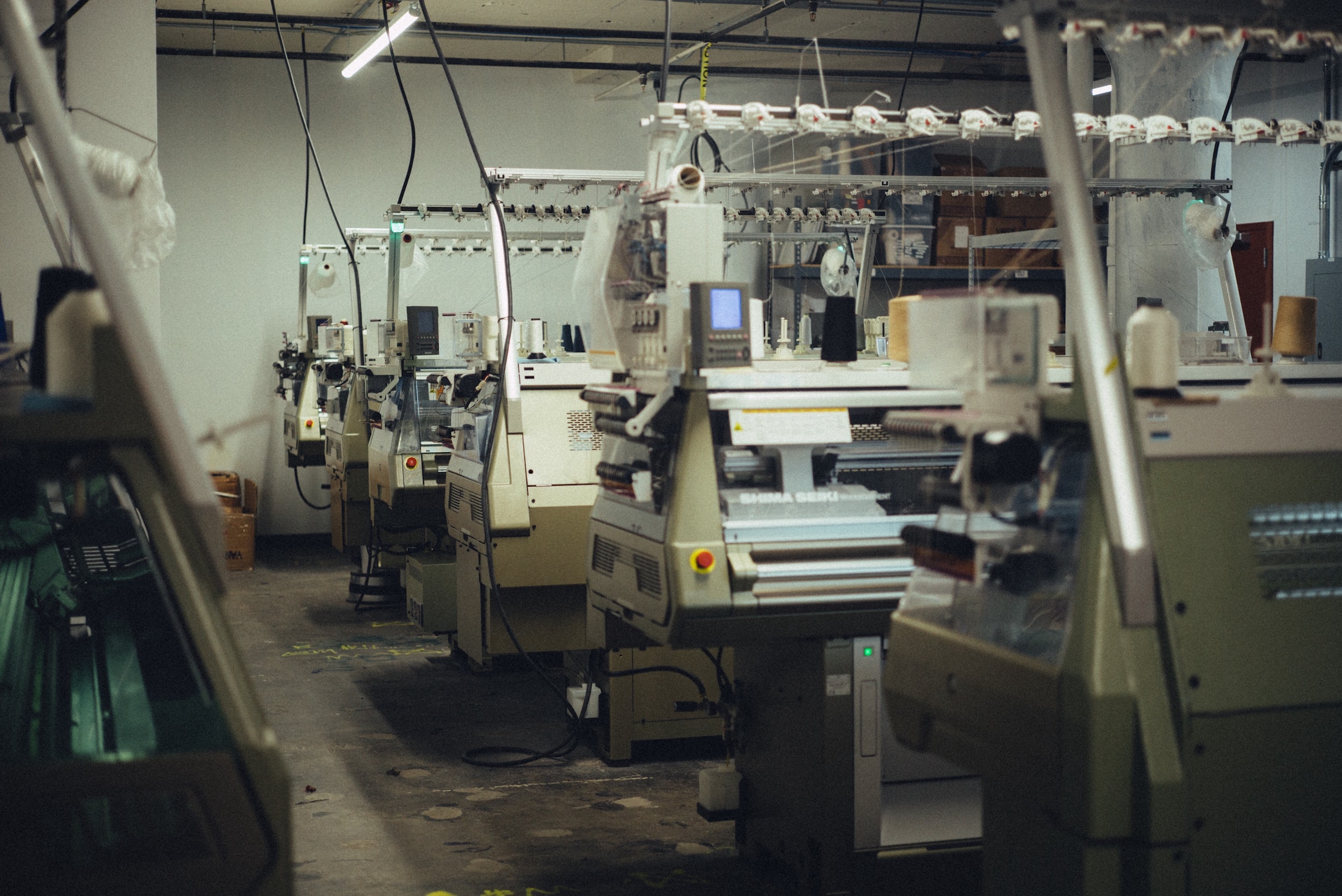
スタジオには、10台のホールガーメント機が所狭しと並んでいる。
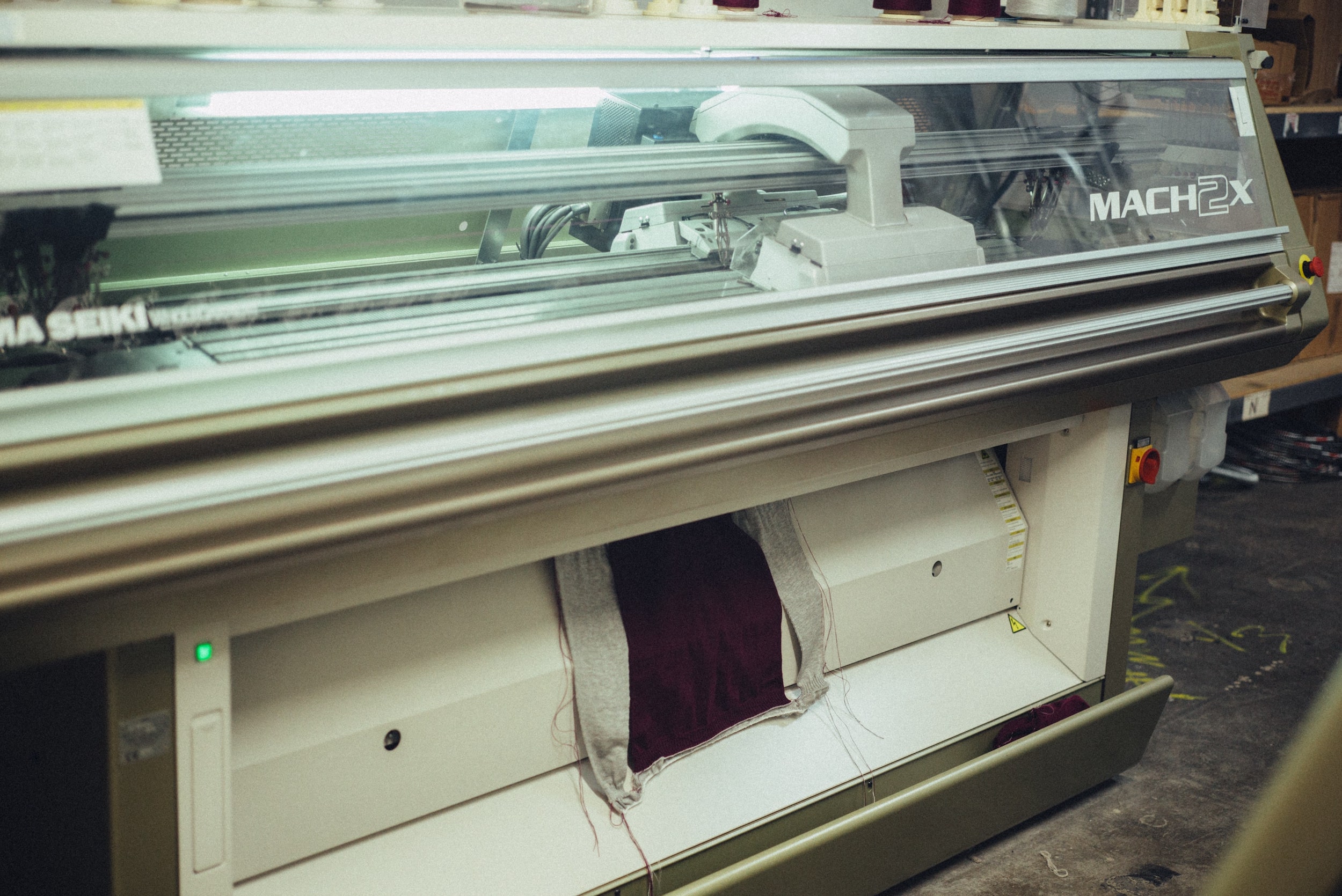
無人でウィーン、ウィーンとフル稼働。編み上がったものが、少しずつ、まるでコピー機のように機械の中から出てくる。
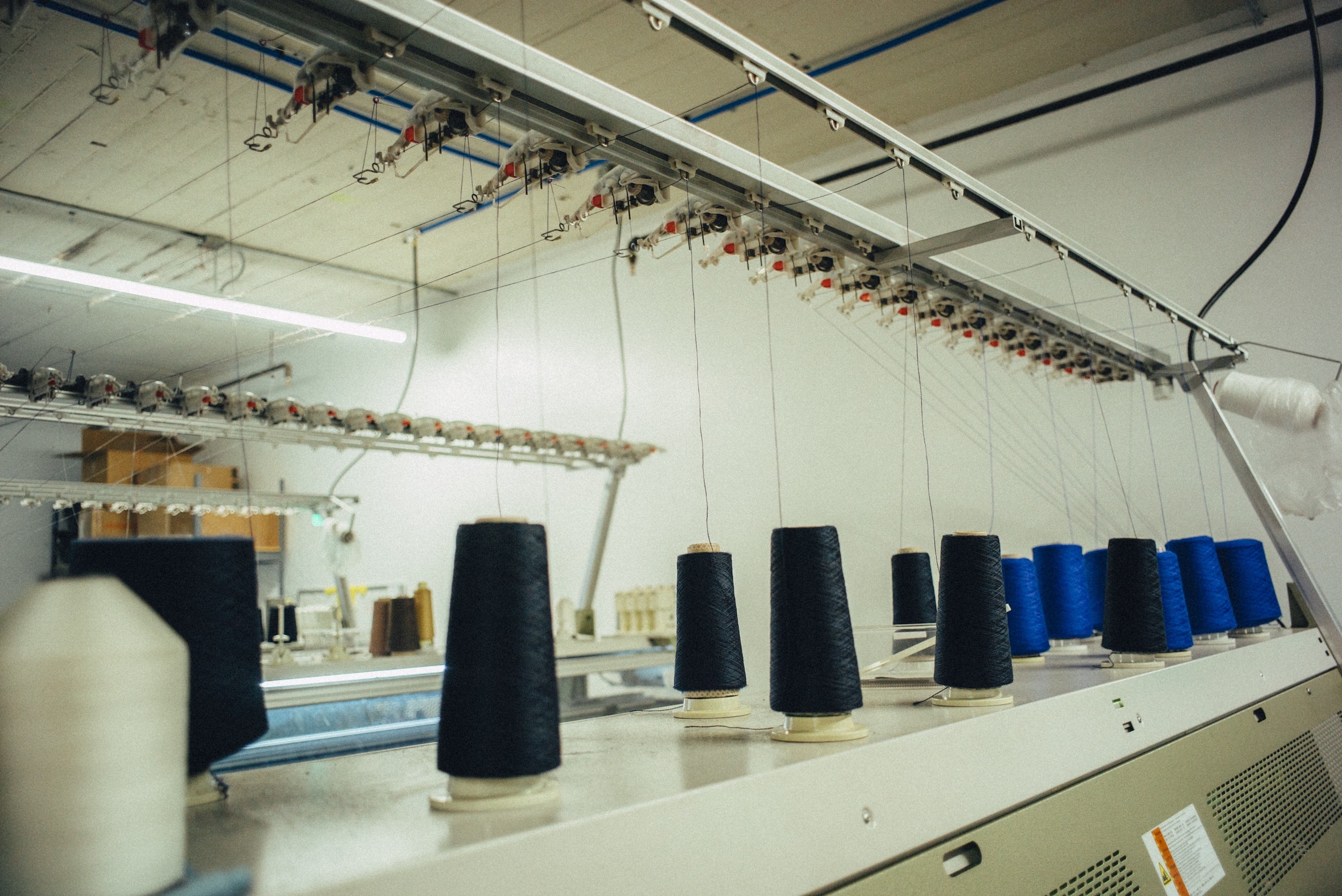
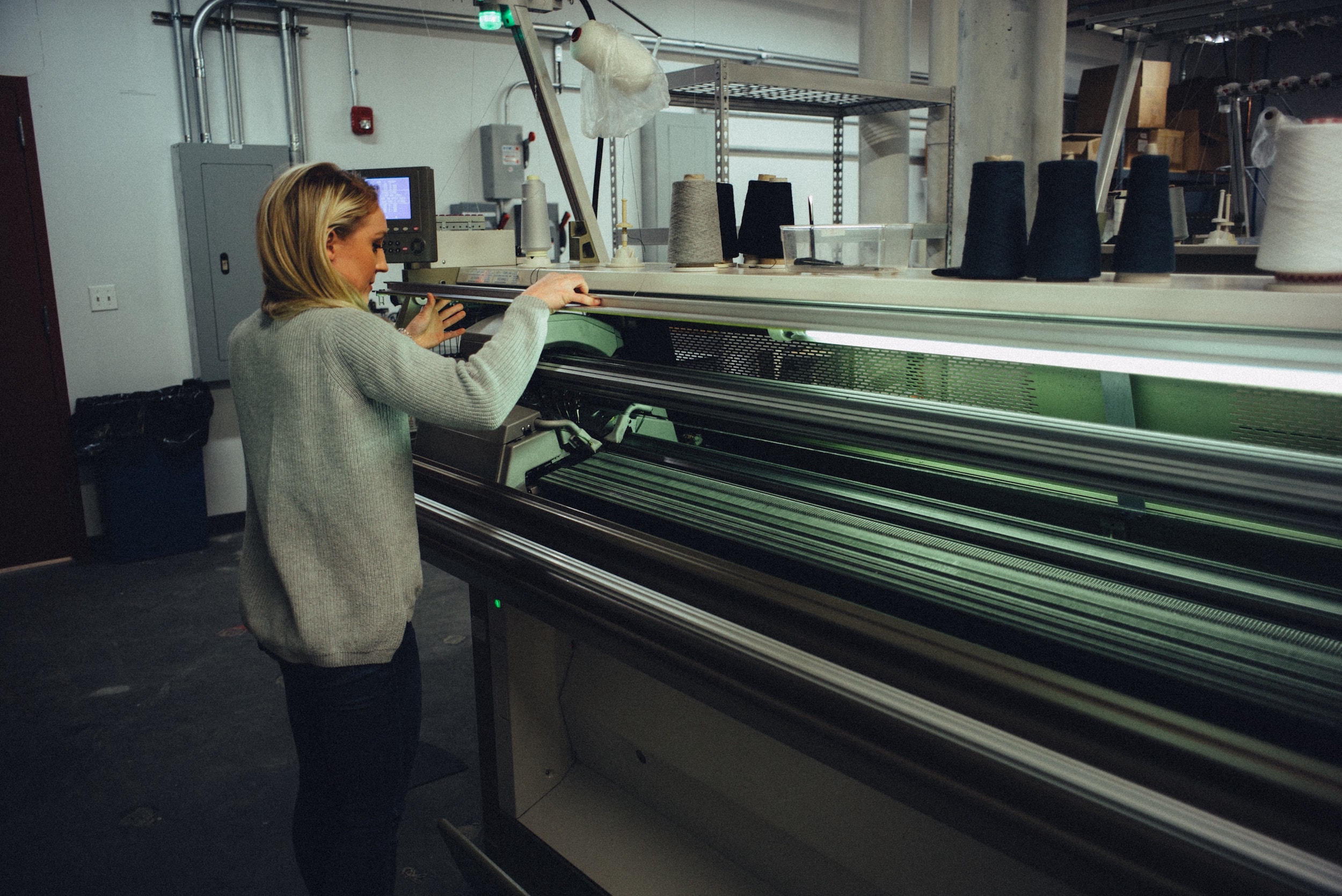
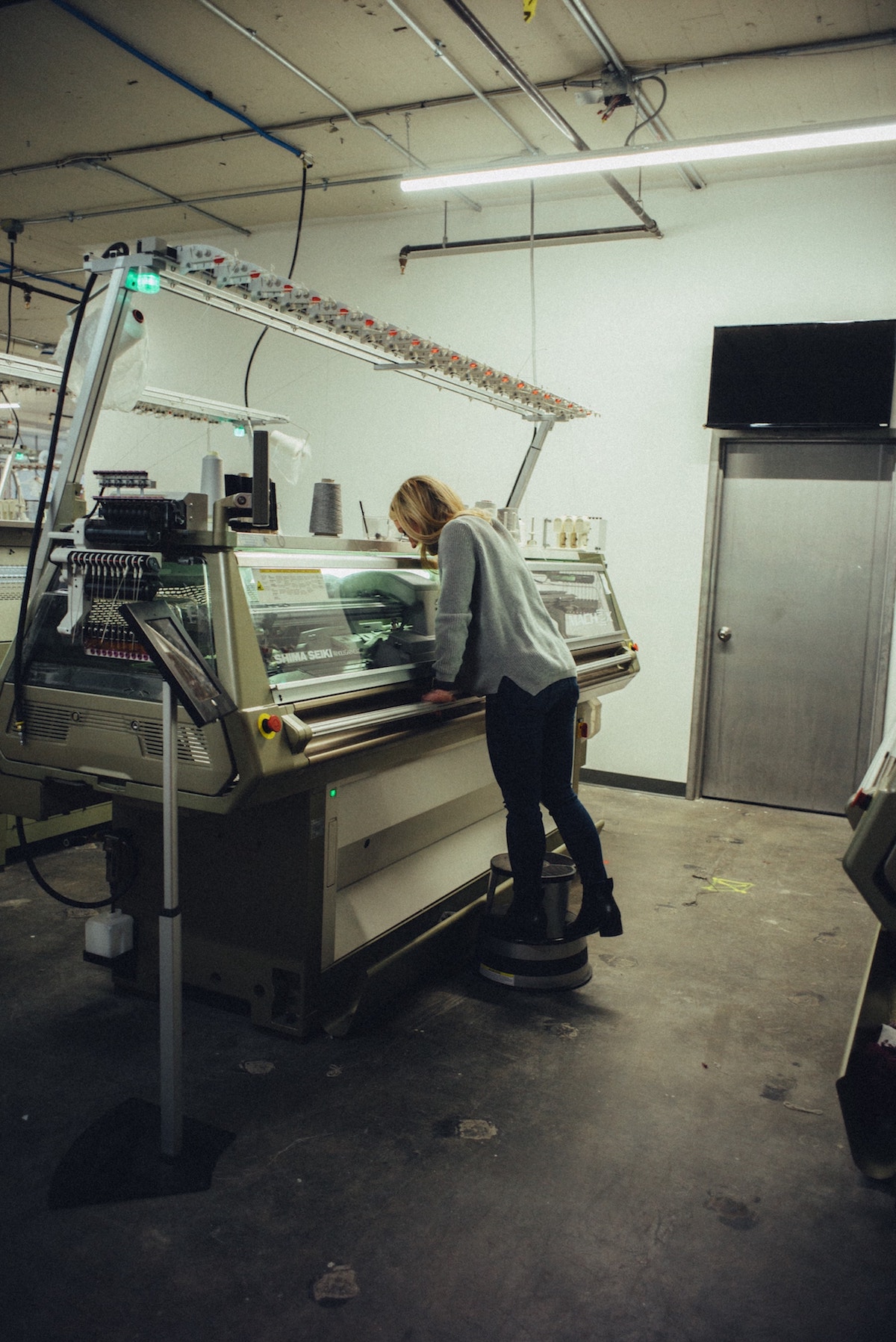
糸がたるんだ・絡まったなど、何らかの問題が発生すると赤いランプでお知らせ。
機械に精通した従業員がやってきて、問題をチェックして手直し。また機嫌を直して、ウィーン、ウィーンと動き出す。
いままでは「服の企画や開発から販売まで、おおよそ半年以上はかかっていました。つまり、ブランド(デザイナー)は半年以上先の流行を先読みしなければならなかったのです。ブランドは半年先の需要予測をもとに縫製工場に発注しているわけですが、予測を的中させるのは至難の技。近年はSNSなどの影響で消費サイクルが速くなっているので尚更です」と、売れ残る余剰在庫の要因について語る。
半年先の需要予測をもとに発注する際には、上述の通り、工場の稼働率が低い場合は製造原価が跳ね上がってしまうので、製造側(工場)もブランドに最低限これだけの量はオーダーしてくださいという「ミニマム」を要求する。となると、発注するブランド側はカケに出るしかない。
売れるかどうかわからないけれど「とりあえず、黒と白と赤とグレーの4色展開で行こう。白と黒は確実に売れるだろう」では、必然的に在庫は生まれる。この、そもそも在庫(無駄)を生むことが前提となってしまっているところに問題があるという。ホールガーメント機を有する同社は「オンデマンド」生産で、ここにテコ入れをする。
オンラインブランドであれば、受注が入ってから2週間でメイド・イン・ニューヨークの商品を国内のエンドユーザーに届けることができるという。実店舗をもつブランドには、シーズン初めに市場に投入する服の量を減らし「売れゆきの良いものを少量ずつ追加発注する」やり方を提案しているそうだ。
色も最初から4色展開する必要はなく、あとから色を追加することもできる。「店舗のロケーションが僕らの製造場であるブルックリンから近ければ近いほど、これも輸送費を省くことで安価かつ迅速に補充可能」と話す。つまり、テクノロジーが発達した21世紀のいま、「アパレル製造を、再び消費の街に返還することができる」という。それが実現すれば、アパレルマイレージ(商品の輸送や運搬に時にでるCO2量)を減らすことができる。
21世紀のオンデマンド生産。製造を再び都市へ、消費の地に戻すメリット
ニューヨークという、数多のファッションデザイナーがひしめく土地に製造を戻すメリットについて、彼はこう語る。「デザイナーやブランドと直にコミュニケーションや商品確認をおこなえるのは大きいと思います。たとえば、スティーブン・アランとのコラボレーションセーターは、企画からマンハッタンの店舗に商品を並べるにかかった時間はたったの2ヶ月です。これも『こういったセーターを置きたい』という声を迅速にキャッチしてサンプルをいち早く見せ、すぐに生産に移ることができたからだと思います」
また、古き良きアメリカを謳った「Made in USA(メイド・イン・USA)」ブランドとの相性も良い。もともと国内で少量生産をしていたブランドにも、近年は消費サイクルの速さから、「販売時期の直前まで、市場動向を見極めたい」という欲求が生まれていた。発注から発送までを約2週間でおこなえる同社はこの欲求にも応えられる。
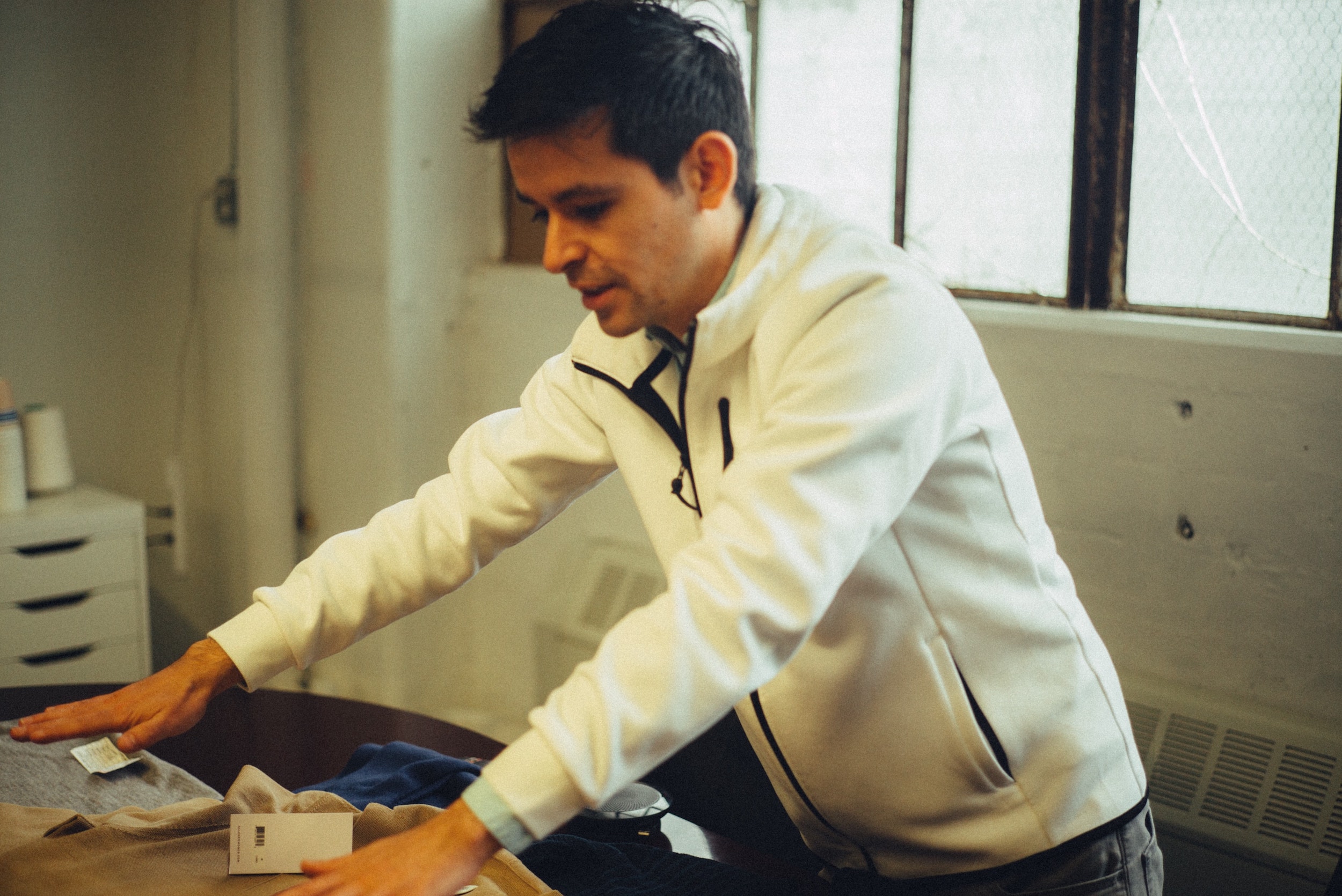
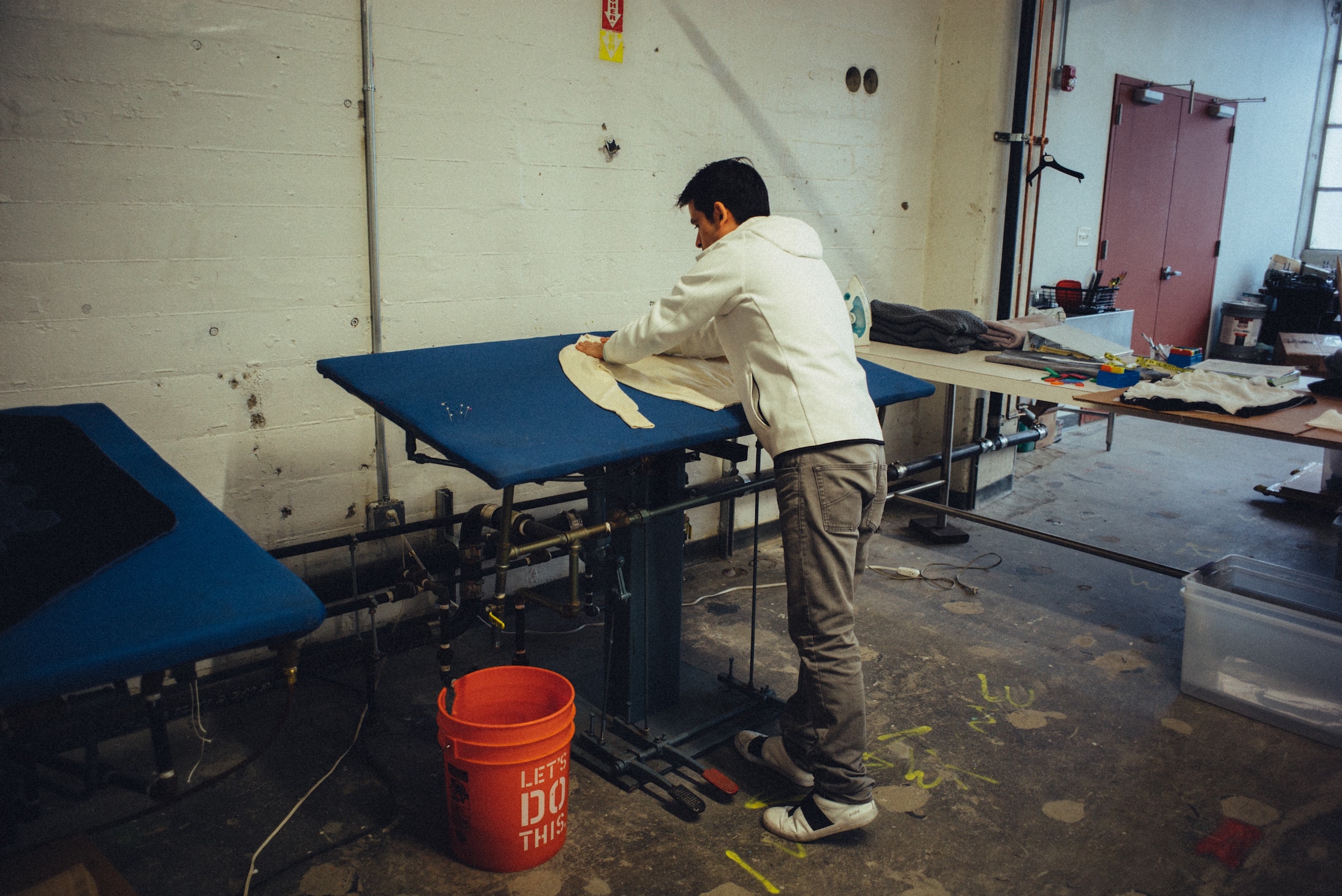
できあがったものにスチームがけ。
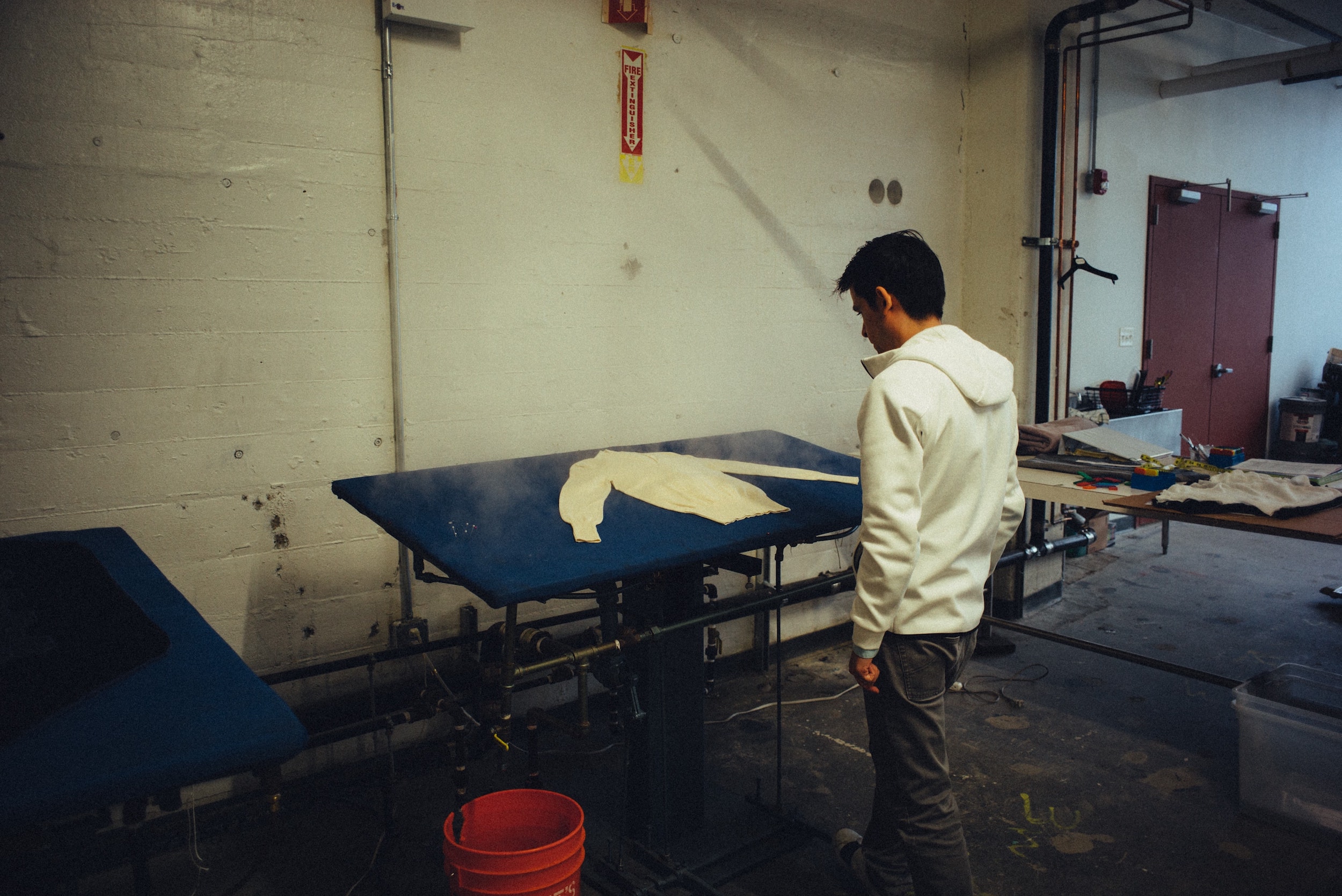
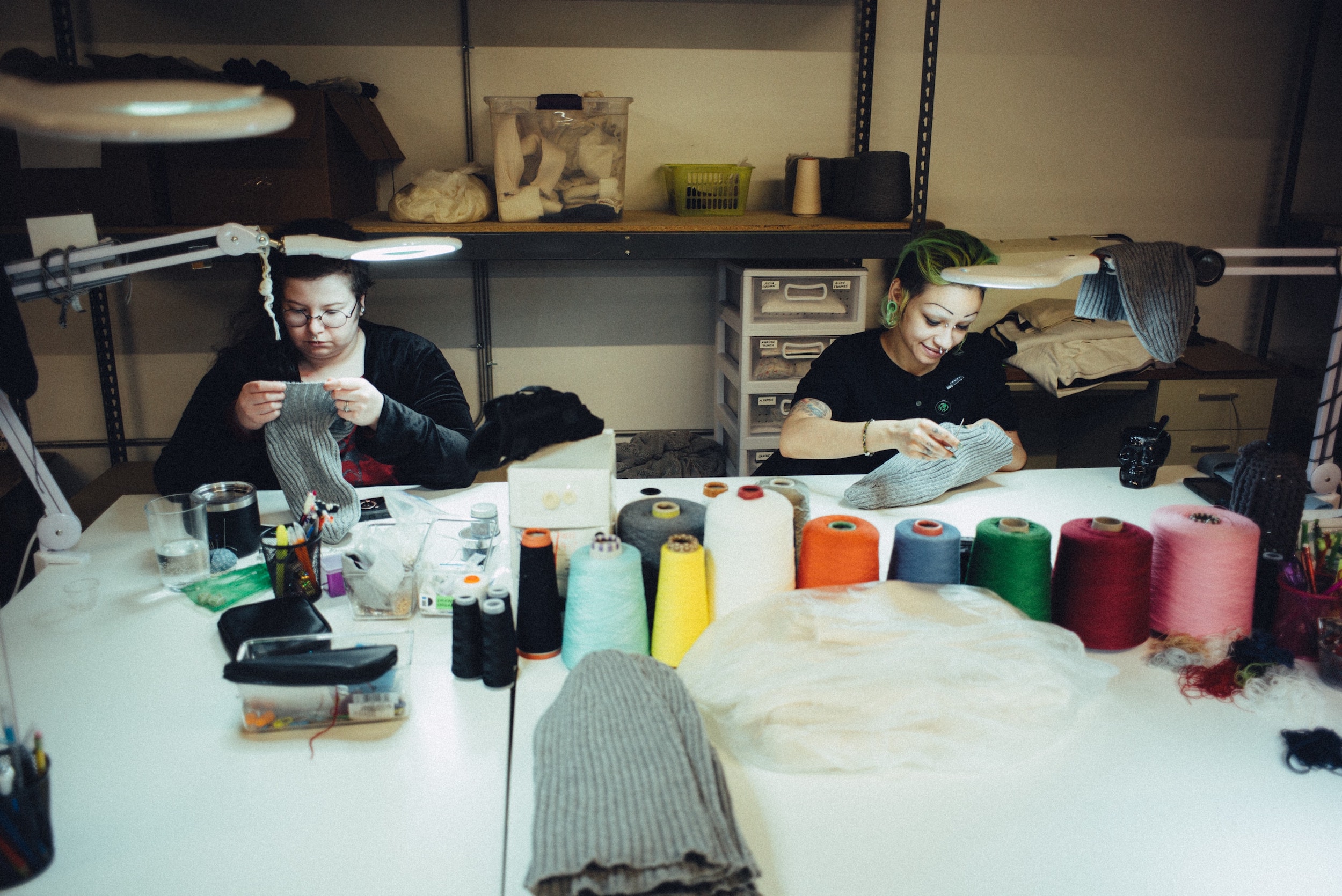
ほつれた部分は人が手直しする。
もちろん、オンデマンド生産は、大量生産システムよりも商品ひとつあたりの生産にかかるコストはややかさむ。だが「在庫をストックする場所代や、最終的に売れ残りを処分する費用など長期的に考えると、決して高額なわけではない」という。むしろ、廃棄や値引きを縮減することで出た利益の一部はメーカーの利益に繋がり、また、コストを削減できたぶんの一部を価格のフィードバックとして提供されれば、消費者もハッピーである。そして、繰り返しになるが、衣類ゴミ問題を根本から解決するこのやり方は、繊維産業において、もっとも持続性の高い生産方法だといえる。
その昔は「〇〇工場」だった建物をリノベートして、ブティックホテルになったり、複合商業施設にになったり——しているブルックリンだが〇〇の部分によく「縫製」が入るのが気になっていた。どうやら「この街は、大量生産時代に入るまでは、アメリカの、そしてファッションの街、ニューヨークのアパレル産業を支える縫製工場の街だった」らしい。サステナブルでより効率的な生産方法が生み出された21世紀のいま、製造業が再び都市に戻ってくる日も近いかもしれない。
Interview with J.Andres Alves, Co-Founder of Tailored Industry
Photos by Kohei Kawashima
Text by Chiyo Yamauchi
Content Direction & Edit: HEAPS Magazine